Metallurgical Technologies, Inc.
Case Study: Metallurgical Failure Analysis of cracked stainless steel heat exchanger tubes
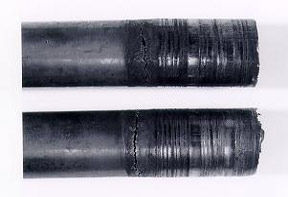
Metallurgical failure analysis and metal corrosion testing services provided by Metallurgical Technologies, Inc. can help minimize and eliminate the undesirable aspects of unexpected down time in the chemical industry. We specialize in rapid response. When the root cause of the metallurgical failure is identified, results are communicated immediately. Recommendations can be made to help prevent future unscheduled events.
Metallurgical Failure analysis of cracked stainless steel heat exchanger tubes
Two cracked 316L stainless steel tubes from a sodium hydroxide heat exchanger were analyzed to determine the cause of cracking. The tubes are 0.750-in. OD x 18 gage specified SA-249, Type 316L. Both tubes exhibit circumferential cracks near the end where they are expanded into the tube sheet.

One of the cracks was opened to examine the fracture surface topography. The opened crack surface was examined at various magnifications using a scanning electron microscope (SEM) as detailed here. The surface appears brittle with several axial crack branches intersecting the circumferential crack plane.

The crack surface exhibited several localized regions of shallow intergranular progression along the ID. The depth of intergranular cracking was only two or three grains deep along the ID. The rest of the surface is mainly transgranular, a characteristic of caustic stress corrosion cracking.

An axial cross-section was taken through the end of the crack and prepared for metallurgical failure analysis to investigate the crack morphology and surrounding microstructure. The crack opening is at the ID surface in a small pit within a zone of shallow intergranular corrosion.

The middle and tip of the crack are transgranular and exhibit multiple crack branches indicative of stress corrosion cracking (SCC).
CONCLUSIONS:
Results indicate the tubes cracked circumferential from the ID surface at the top of a tube sheet expansion due to caustic stress corrosion cracking (SCC). The circumferential cracks initiated in small patches of intergranular corrosion in the ID surface. The main cracks were transgranular with multiple branches which are characteristics of stress corrosion cracking in austenitic stainless steel. Reported temperatures indicate the tube wall is within the temperature range of susceptibility to caustic SCC. Residual stresses from the expansion process resulted in tensile stresses on the tube ID slightly above the upper edge of the expansion transition.
Higher nickel alloys such as Inconel 600 or 690 exhibit superior resistance to caustic SCC (stress corrosion cracking) at expected operating temperatures and should be considered as alternate tubing materials.
Forensic examination of a failed component can prevent recurring failures, help with preventive detection, and suggest remedies. If you have a component failure that you would like investigated, just take a moment to fill in our information request form and we'll gladly give you an estimate.
Click here for more Product Details from
Metallurgical Technologies, Inc....