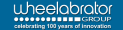
Contact Details:
Wheelabrator
1606 Executive Drive
LaGrange
GA
30240
United States of America
Tel: +1 706 884-6884
Fax: +1 706 884-0568
Send Enquiry | Company Information
Shot Peening Technology improves Standard Steel operations
Product News Monday, August 3, 2009: Wheelabrator
Standard Steel, located in Burnham, Pa., is a leading manufacturer of forged steel wheels and axles in a variety of sizes for the freight, locomotive and passenger/ transit railway markets. As the sole producer of forged steel wheels for railcars and locomotives in North America, the company has been in operation since 1795. The company has experienced several name changes; however, one thing that remains consistent is its commitment to quality.
Prior to contacting Wheelabrator Group in 2004, Standard Steel was already operating two (2) older Wheelabrator® Shot Peening machines. The company approached Wheelabrator Technical Sales Representative, Jay Benito, to discuss replacing their current shot peening equipment. Throughout discussion with Wheelabrator technical and engineering personnel, the company was looking for an up-to-date, maintenance-friendly system that would modernize their daily operations. They were looking to upgrade one (1) of their two older models. Analyzing their needs closely, in particular taking into consideration existing facility and pit parameters, a decision was made to purchase a new 2-Wheel Shot Peening machine. When production levels significantly increased in 2007, Standard Steel placed a repeat order for the same machine to remain competitive and to keep up with demand. With the addition of the two (2) new machines, both with EZEFIT® wheels, the company has experienced a reduction in both their peening cycle times and maintenance costs.
The process of forging is shaping heated metal in a die under extreme pressure, while the casting process involves pouring molten metal into a mold. Modern passenger train cars require forged steel wheels for improved safety. These wheels are shot peened to a specified industry standard for improved resistance to fatigue cracking under rolling stresses. The process of shot peening extends the overall lifespan of the wheels. “The two (2) new machines have not only significantly reduced maintenance costs, but have also reduced downtime and have easily kept pace with an approximate 30 percent increase in wheel productivity.” said Mr. Jeffrey L. Richardson, Project Manager at Standard Steel.
Forged wheels are loaded by a forklift operator, onto a declining rail entrance conveyor. The operator manually controls the opening of the entrance doors to the blast cabinet, where the forged wheels (positioned upright) are rotated for 45-50 seconds in front of two blast wheels. The EZEFIT blast wheels shot peen both sides simultaneously with S660 hardened steel shot. At the end of the peening cycle, the exit doors slide open, allowing the forged wheel to be pushed onto an exit rail conveyor where the same forklift operator retrieves the peened wheel, taking it to its next stage, inspection. Equipped to run for multiple shifts; machine production is approximately 60 forged wheels/per hour.
In 2007, personnel from Standard Steel attended the wet-run test of the wheel shot peening system at the Wheelabrator Technology Centre, based in Burlington, Ontario. This was to ensure a smooth installation and start up at the company’s plant. Both machines continue to be important contributors to Standard Steel’s daily operations in meeting their customers’ cleaning requirements.
Wheelabrator Group is a global provider of surface preparation and finishing solutions. Committed to offering the broadest array of technologies, products, replacement parts, services and technical know-how, Wheelabrator Group works closely with customers to deliver the best solutions for their specific requirements. The company''s strategically located and electronically linked offices allow Wheelabrator Group to provide unrivalled customer service and support worldwide.