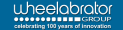
Contact Details:
Wheelabrator
1606 Executive Drive
LaGrange
GA
30240
United States of America
Tel: +1 706 884-6884
Fax: +1 706 884-0568
Send Enquiry | Company Information
Proven and Effective Wheelabrator Surface Preparation Solutions for Shipyard
Product News Tuesday, September 1, 2009: Wheelabrator
The Shipyard industry continues to provide Wheelabrator with a variety of surface preparation opportunities. Raw materials and finished assemblies from manufacturing processes have challenged Wheelabrator to develop and perfect automated cleaning and coating systems for large sized, heavy plates and structural steel. The extensive global base of Wheelabrator customers in this sector regularly use Wheelabrator® equipment to blast clean, impart a surface profile, paint and cure such components, to assure corrosion protection. Similarly, large assemblies get treated in manual blast and paint facilities.
Wheelabrator thoroughly understands the critical nature of the steel coating process in shipbuilding. Multiple, strategically positioned airless, centrifugal blast wheel units clean all areas of steel plates and profiles to remove rust and mill scale prior to coating. Brush-off and blow-off systems remove residual abrasive from the parts and prevent their entry into the coating chamber. Paint guns, mounted on high-speed, automatic reciprocators coat the parts with weldable, zinc-based primer to facilitate storage without the threat of corrosion. Such systems are classified by Wheelabrator as Preservation Lines (PRL series).
Wheelabrator Plate and Structural machines are available to handle a range of work up to 15 ft. wide plate and 18” high structural steel. Larger and smaller part dimensions can also be accommodated with minor modifications. Wheelabrator EZEFIT® and AutoBlast® centrifugal blast wheels contribute to increased productivity resulting in line speeds as high as 20 feet per minute with the right combination of motor HP. These machines are commonly integrated into Wheelabrator Preservation Lines.
When the size of a fabricated assembly makes it impractical for automated blast cleaning and coating, Wheelabrator Airblast and Paint Rooms provide the optimum solution. These rooms are configured for single or multiple operators. Different styles of work flow can be configured based on material flow at individual customer locations. Airblast and Paint rooms are properly illuminated and ventilated with Wheelabrator Dust Collectors, as per commonly accepted codes such as ACGIH and OSHA. Wheelabrator engineers can also design work handling systems such as powered and manual work cars to convey the parts.
Wheelabrator Group is a global provider of surface preparation and finishing solutions. Committed to offering the broadest array of technologies, products, replacement parts, services and technical know-how, the Wheelabrator Group works closely with customers to deliver the best solutions for their specific requirements. The company's strategically located and electronically linked offices allow Wheelabrator Group to provide unrivalled customer service and support worldwide.